Una pareja perfectamente compenetrada: ¿cómo emparejamos los motores Kawasaki con las máquinas que impulsan?
3 jul 2023 Engines & Aftercare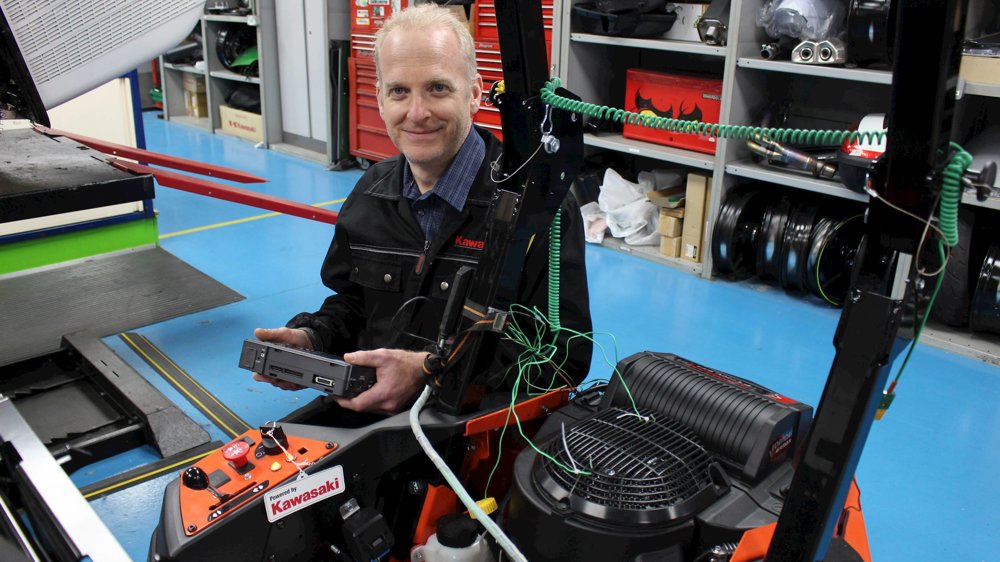
Alan Lunn, ingeniero de aplicaciones de Kawasaki Engines UE, es el responsable de perfecta integración entre los motores y los equipos. Explica el proceso y los retos que esto conlleva y nos desvela cómo colabora Kawasaki con los fabricantes para garantizar la calidad.
Aunque un motor es un elemento integral del rendimiento general de un equipo, necesita emparejarse con una máquina de igual calidad para destacar.
El proceso de emparejar el motor adecuado con un equipo concreto —y garantizar que todo funciona sin problemas— se conoce como «ajuste del motor». Nuestro ingeniero de aplicaciones Alan Lunn es el responsable de esta parte vital de la fabricación de un producto final excepcional.
Alan atesora una vasta experiencia en el ámbito de la ingeniería y, tras haber trabajado en Kawasaki Motors durante muchos años, no hizo la transición al mundo de los cortacéspedes y los equipos de paisajismo hasta hace relativamente poco. Aporta a su puesto una experiencia y unos conocimientos técnicos únicos y viaja por todo el mundo para ayudar a que los proyectos se hagan realidad.
Hablamos con Alan para que nos desvele lo que hay entre los bastidores del proceso de ajuste del motor y cómo garantizamos que el equipo de nuestros clientes rinda al máximo nivel.
Entonces, ¿por dónde se empieza cuando hay que adaptar un motor a una máquina?
Se empieza por determinar claramente qué es lo que espera del motor el fabricante del equipo. Un fabricante de equipos originales, también conocido como OEM por las siglas en inglés, ha diseñado una máquina y necesita un motor que la impulse. Puede que estén diseñando un nuevo cortacésped de giro cero, un tractor cortacésped... o, si se trata de un cortacésped con control remoto, va a necesitar de su motor cosas muy diferentes de las que hacen falta en un cortacésped de empujar.
Debatimos con el OEM el tipo de aplicación y el sector del mercado al que está destinada —el uso profesional industrial requiere un motor diferente al del uso residencial ligero— y eso nos da una idea de la serie de motor Kawasaki que van a necesitar. Así podemos seleccionar el motor con las características de potencia más adecuadas: para un trabajo realmente difícil, por ejemplo, podríamos proponer un motor FX. El OEM puede tener en mente sus propias expectativas y una idea del precio que está dispuesto a pagar, por lo que lo verdaderamente importante es encontrar el equilibrio adecuado.
¿Qué ocurre después de haber seleccionado un motor para un equipo?
Una vez que encontramos un motor que se puede sugerir, suelo enviar dibujos de modelos CAD en 3D que se lo muestran todo al fabricante con mucha claridad. Así, él puede utilizar estos modelos para seguir desarrollando su nueva máquina prestando especial atención a las holguras, los mazos de cables, las tuberías y la toma de fuerza.
A menudo, el equipo técnico de los departamentos de I+D es con quien más trabajo. Ellos desarrollan y diseñan los productos, y es en este momento inicial cuando quieren que el motor encaje en la máquina para asegurarse de que todo funciona. Y lo quieren desde el principio, es decir, quieren que el motor esté ahí mientras fabrican el chasis.
Una vez superada esta fase inicial, podemos organizar el envío de un motor de muestra para su ajuste y las pruebas posteriores. En este punto, las pruebas empiezan a ser un poco más exhaustivas y se examinan las emisiones del sistema de escape para asegurarnos de que cumplen las normativas de los distintos países a los que se puede exportar la máquina.
A continuación, organizo una visita al OEM para supervisar o realizar una «comprobación de coincidencia», es decir, una evaluación del ajuste y el funcionamiento. Aparte de un examen muy profundo de las interfaces y holguras entre el motor y la máquina, esto también implica la colocación de varios termopares alrededor del motor para luego ponerlo en funcionamiento a carga máxima durante un tiempo determinado.
A lo largo de este proceso, controlo las temperaturas del motor para asegurarme de que no superamos determinadas cifras y, en caso de que sea de inyección de combustible, vigilo los parámetros que registra la unidad electrónica de control (ECU) para garantizar la fiabilidad del motor en las condiciones más exigentes. También evalúo la facilidad de acceso para el mantenimiento del motor.
Toda la hoja de ruta de ajuste del motor, desde los conceptos iniciales hasta el momento de dar el visto bueno antes de la producción del equipo, puede durar unos 13 meses.
¿Hay algún aspecto problemático en el proceso?
He tenido suerte, ¡hasta ahora no me he encontrado con grandes problemas! Anteriormente sí habíamos sufrido algunas situaciones delicadas: una de las que recuerdo fue un problema con el flujo de aire al motor. En los cortacéspedes de giro cero, el motor está situado en la parte trasera de la máquina, donde está muy bien ventilado. En este caso, se trataba de un tractor cortacésped con un flujo de aire mucho más limitado, por lo que hubo que hacer modificaciones para incrementar la ventilación y que todo funcionara sin problemas.
Hacemos modificaciones si es técnicamente necesario o también si el OEM especifica cosas que quiere cambiar, añadir o eliminar en un motor estándar. Si estos cambios están a nuestro alcance, entonces construimos un motor de muestra a medida. Si se consigue el resultado deseado, la nueva especificación puede pasar entonces a la producción.
¿Puede hablarnos un poco más de usted? ¿Cómo llegó al ámbito del montaje de motores?
Siempre he sentido inclinación por trabajar con máquinas y tecnología. Como muchos otros niños, estaba constantemente desmontando cosas para ver cómo funcionaban, con la única diferencia de que... ¡podía volver a montarlas!
Tras formarme como técnico de motocicletas y ascender a jefe de taller en varios concesionarios, me incorporé a Kawasaki Motors UK, donde pasé muchos años trabajando como asesor técnico y de atención al cliente. Con el tiempo sentí la necesidad de buscar un nuevo reto, lo que llegó en forma de mi nuevo cargo de ingeniero de aplicaciones en Kawasaki Engines UE.
Ha sido un cambio emocionante para mí, ahora trabajo en una faceta mucho más práctica. Me reúno regularmente con asesores técnicos en EE. UU. y viajo por todo el mundo colaborando con diversos fabricantes de equipos originales. Es fantástico ver las relaciones duraderas que se han desarrollado entre los fabricantes y me siento privilegiado de formar parte de ello.
¿Cómo se asegura de que el ajuste final cumpla los estándares de Kawasaki?
Puedo pasarme un día entero con el OEM haciendo repetidas pruebas como parte del proceso de «comprobación de coincidencia». Por supuesto, ¡ellos están tan interesados como nosotros en que la máquina rinda a la perfección! Todos los implicados están deseosos de crear algo que sea de primera calidad en todos los sentidos, y el objetivo es encontrar un motor de primera calidad para un producto de primera calidad.
En cuanto a las pruebas en sí, las llamamos «comprobación de coincidencia». Sobre todo, buscamos asegurarnos de que la aplicación no va a destrozar el motor: hay todo tipo de cosas que podrían causar daños potenciales, como por ejemplo la falta de flujo de aire. Es un proceso minucioso que llevamos a cabo tanto yo como uno de los miembros del personal del fabricante del equipo. Su departamento suele haber hecho ya entre 70 y 80 horas de pruebas antes de mi llegada.
En lo referente al cumplimiento normativo, somos responsables del motor y nos tomamos este papel muy en serio. Hacemos todo tipo de pruebas en nuestras instalaciones de producción de EE. UU. para asegurarnos de que el motor cumple la normativa, así como para evaluar su rendimiento. Cuando llega el momento de montar el motor, me fijo sobre todo en el cumplimiento normativo de las emisiones.
Hacemos una prueba completa del silenciador, miramos las emisiones generales de escape, las cifras de contrapresión, el consumo de combustible, las temperaturas de los gases de escape... todo lo que está en nuestra mano. Rara vez surgen problemas en esta fase, al menos según mi experiencia, ya que el proceso previo de planificación es muy minucioso.
¿Alguna última reflexión que compartir sobre el proceso de montaje del motor?
Supongo que la fiabilidad es la clave de todo: los motores Kawasaki están diseñados para soportar la máxima carga de trabajo y, en consecuencia, se someten a las condiciones más exigentes a las que podrían enfrentarse en una situación real. En resumen, estamos suministrando un componente de alto rendimiento en estrecha colaboración con el OEM, pero la confianza es bidireccional y, en última instancia, está en manos del OEM integrar nuestro motor y crear una máquina de calidad superior. Ambas partes deben valorar la calidad, y por este motivo trabajamos con OEM que diseñan equipos excepcionales.
¡Gracias por su tiempo y sus interesantes comentarios, Alan! Para ver el resultado de este trabajo y los OEM con los que trabajamos, visite la página Powered by Kawasaki.
You may be interested in
-
¿Cuánto duran los motores Kawasaki?
-
¿Cómo garantizamos la calidad en Kawasaki Engines? Una mirada entre bastidores a nuestras plantas de fabricación en EE. UU.
-
Mantenimiento de motores de cuatro tiempos: guía práctica
-
Piezas originales de Kawasaki Engines y piezas del mercado posventa no originales: ¿cuál es la diferencia?
-
Encuentre la diferencia: una comparación directa entre piezas originales y piezas del mercado posventa.
-
Winter pre-storage preparation for your Kawasaki powered equipment